Fibre Advancements
- sustained.style
- Apr 23, 2020
- 12 min read
There are many fibres which everyone is familiar with – wool, cotton, silk, linen, polyester, acrylic and nylon, to name a few. This week we’re analysing the eco-friendliness of these familiar fibres and exploring the more sustainable alternates which are emerging in the textiles and fashion industries.
Synthetic fibres, such as polyester, acrylic and nylon, are all created through a similar method, using heat as a catalyst to chemically bond various monomers – commonly an acid and alcohol – in a process called ‘polymerisation’. The resultant mixture is cooled in ribbons, before being cut into small chips. The chips are then re-melted, and can be dyed in their liquid state, after which the fibres are extruded from spinnerets as filaments.
Synthetic fabrics do not decompose – instead, breaking down into microplastics which bioaccumulate through the food chain
The resources needed to create synthetic fabrics, such as petroleum, are non-renewable, and often have high levels of toxicity, which contaminate ecosystems and harm biodiversity
Nitrous oxide and other greenhouse gases are released into the atmosphere during polymerisation, contributing to global warming and creating acid rain
Synthetic fibres can be recycled into new materials of equal quality
Left to right: Synthetic filaments being extruded from a spinneret, and a diagram showing various methods of spinning synthetic fibres.
Regenerated cellulose fibres, including acetate, viscose, rayon, modal, lyocell, Tencel, are manufactured using similar processing methods, which transform wood pulp – from sources such as bamboo, eucalyptus and beech trees – into fibres. This is achieved by first crushing the material source, then chemically dissolving plant’s cellulose with chemicals such as sodium hydroxide and carbon disulphide, or non-toxic solvents, creating a viscose cellulose solution which is extruded from spinneret nozzles into dilute acid solution to solidify as continuous filaments. The fibres are then utilised to weave or knit fabrics that tend to have similar qualities to silk and cotton.
While some regenerate cellulose fibres utilise harmful chemicals, closed-loop manufacturing processes can be employed to capture and recycle 99.5% of chemicals
Different wood pulp sources require varying quantities of resources, although the selected species generally need minimal amounts of water, pesticides and herbicides, limiting the environmental impact of chemicals and water scarcity
Deforestation for plantations is common, and causes a decrease in biodiversity, displacing animals from their habitat, as well as releasing stored carbon into the atmosphere, where it accelerates global warming
Left to right: Bamboo, which is a source of cellulose for regerated fibres, bamboo viscose fibres, and white bamboo viscose fabric.
Natural protein and cellulose fibres are generally considered preferable to those that are man-made, as they are biodegradable, however, the chemicals used for dyeing and finishing processes are retained by the fibres and distributed into the environment as they decompose. The chemically heavy process of synthetic dyeing can be eliminated when using natural fibres – particularly protein compositions – as the fibres readily absorb natural dyes, which biodegrade harmlessly with the material. An additional advantage of natural fibres is their ability to store atmospheric carbon throughout the garment’s lifespan, preventing the release of greenhouse gases into the atmosphere.
Wool, a natural protein fibre, is sourced most commonly from sheep, but can also be obtained from goats, rabbits, and camelids (alpacas, llamas, etc). The fibre is sheared from the animal – usually by hand – then graded and sorted for quality, and cleaned in alkali baths to remove contaminants. Next, the wool fibres are blended together in a process called ‘carding’, and can also be combed to remove shorter pieces and ensure the fibres are parallel. The wool can then be spun into yarn, dyed, and turned into fabric.
Approximately 500,000 litres of water are necessary to manufacture a metric ton of wool, contributing to the scarcity of fresh, uncontaminated water
The need for grazing pasture results in deforestation – destroying ecosystems, decreasing biodiversity, and causing increases in soil salinity and erosion
Sheep release methane – a gas which traps atmospheric heat, resulting in global warming – at a rate of approximately 25 litres per day
Genetic engineering and selective breeding practises are being utilised to reduce the quantity of methane produced by sheep in an attempt to increase the sustainability of wool production
The shearing process can be harmful to the animals, so wool is not considered appropriate for vegans
Left to right: Sheep grazing in pasture, a man sheaing a sheep, and a bundle of washed, raw wool fibres.
Cotton is the most commonly used natural fibre, accounting for 27% of all fibres utilised for textiles in 2015. Cotton is cellulosic, and is the fluffy, white lint found inside cotton bolls, which are the fruit of cotton plants. The fibres are harvested either by hand or large mechanical harvesters. They then undergo a ginning process, separating the seeds from the fibres, which can then be spun, dyed, and knitted or woven.
Cotton relies heavily on harmful pesticides and fertilisers, which contaminate the soil and water, endangering aquatic biodiversity downstream through direct toxicity or bioaccumulation
Soil used to cultivate cotton is severely degraded due to the plant’s consumption of valuable nutrients
Cotton also has very high levels of water consumption, requiring 20,000 litres of water to produce 1 kilogram of cotton
Organic cotton has a significantly reduced impact on the environment, using 91% less water and no synthetic pesticides

A cotton crop, showcasing the white, fluffy cotton boll fruits.
Silk is spun by the larvae of Bombyx mori – the domestic silkmoth – as a cocoon for metamorphosis into its adult form. The cocoon is formed from one continuous strand of silk, measuring up to 1.6km in length, which is extruded from specialised salivary glands on the pupa. The cocoons – still containing the living pupa – must be boiled or steamed, before being sorted by the characteristics of their fibre. They are then boiled again to soften and remove a gum-like protein, after which any loose fibres will become apparent, and be removed in a process called ‘deflossing’. The cocoon is then unravelled – commonly by machine – and reeled into strands consisting of 2-20 silk filaments, which are twisted, before being dyed and used to create fabric.
Silkworms feed on leaves from mulberry trees, which require very few pesticides or fertilisers to grow, but have a moderate water consumption
The process has a low yield for its input, requiring 104 kilograms of mulberry leaves, eaten by 3000 silkworms, to produce 1 kilogram of silk
Silk production is predominantly isolated to India and China, which incurs pollution from global transportation
Silkworms can have dyes incorporated into their diet, resulting in the extrusion of a coloured silk fibre, which eliminates the need for dyeing processes and reduces water consumption
Peace silks allow the moth to hatch before harvesting the silk, creating a vegan option
Left to right: A silkworm eating mulberry leaves, accompanied by silk cocoons, silk cocoons on racks, and cream-coloured silk satin fabric.
Linen fabric is sourced from the fibres of flax plants, which must be harvested, either mechanically, or by hand, with the plant entirely intact to retain fibre quality. The plant is then stripped of its seeds and leaves, and goes through a process called ‘retting’ – the decomposition of the bark and gum which conceals the flax fibres. This can be achieved through submerging the plant material in water for up to a fortnight, however, commercially it involves baths of alkali or oxalic acid increase the efficiency of the process. The stalks are then crushed, allowing the flax fibres to be released and separated from the bark, which is discarded. Finally, the flax can be spun into yarn, dyed, and utilised for fabric.
Flax plants often require herbicides – as they are easily overwhelmed by weeds – and occasionally pesticides, which pollute the soil and water
The plants are capable of growing in poor soil, rarely requiring fertilisers
The by-products of flax can be utilised, including the use of seeds to make Linseed oil, reducing waste
Where retting is performed using chemicals, the water and bio-waste are contaminated, which can pollute the environment if runoff or decomposition occur.
Flax is naturally beige, therefore bleaching is required where non-natural colours are desired, introducing more chemicals which can potentially harm the environment
Left to right: A flax crop while flowering, manual crushing (decortication) of flax stems, and beige linen fabric woven from flax.
Leather is made from the hide of animals, particularly cows, which is ‘tanned’ – a process which preserves the hide, preventing decomposition – using chromium salts in large water baths. The leather is then dried, after which the tanning process is repeated, and finally, the leather is dyed and finished.
As with wool production, deforestation for grazing pasture is necessary
The animals, predominantly cows, which are used for leather, all generate methane, producing up to 500 litres daily
Tanning processes involved in leather production have high toxicity levels, with chromium – a carcinogen – as well as, lead, arsenic and acids present in the outflow, consequentially polluting the environment
Leather has a high water consumption, both from the animals and processing baths, requiring approximately 17,093 litres per kilogram of the material
The leather industry also generates material waste, as damaged sections of hides – from cuts or grazes sustained by the animal – cannot be utilised
Leather is generally a by-product of the meat and dairy industries, preventing the waste of animal products from these sources
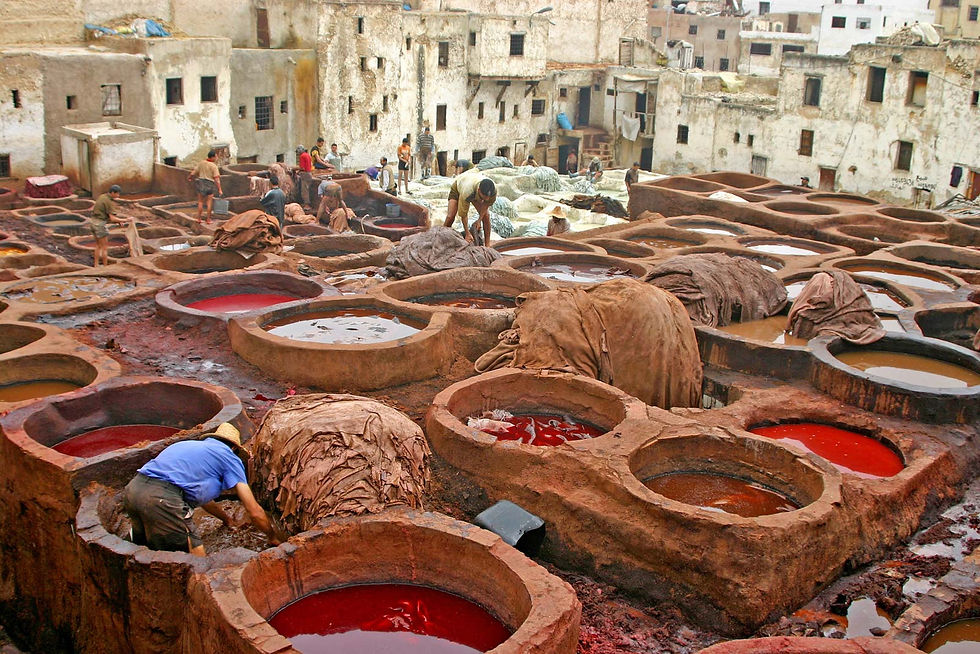
Tradiational Moroccan tanning and dye baths for leather, with many different dye colours and mounds of processed leather.
Hemp, a member of the cannabis family, is produced in through the same process as flax. To some, it has negative connotations due to its biological proximity to marijuana, however, in the textiles industry, it can be regarded as a more sustainable alternative to cotton, and even linen.
The density and hardiness of hemp plants means that they outgrow weeds and therefore don’t require herbicides
Hemp is largely pest-resistant, utilising low quantities of pesticides, if any
The plants are capable of growing in a variety of soil qualities and have the added benefit of returning 60-70% of nutrients to the earth
The density at which hemp grows, in combination with its high fibre output ratio, results in double the yield per hectare when compared to cotton
Hemp has a minimal water consumption, requiring half that of cotton to grow, and ¼ of the water needed to manufacture cotton fabric
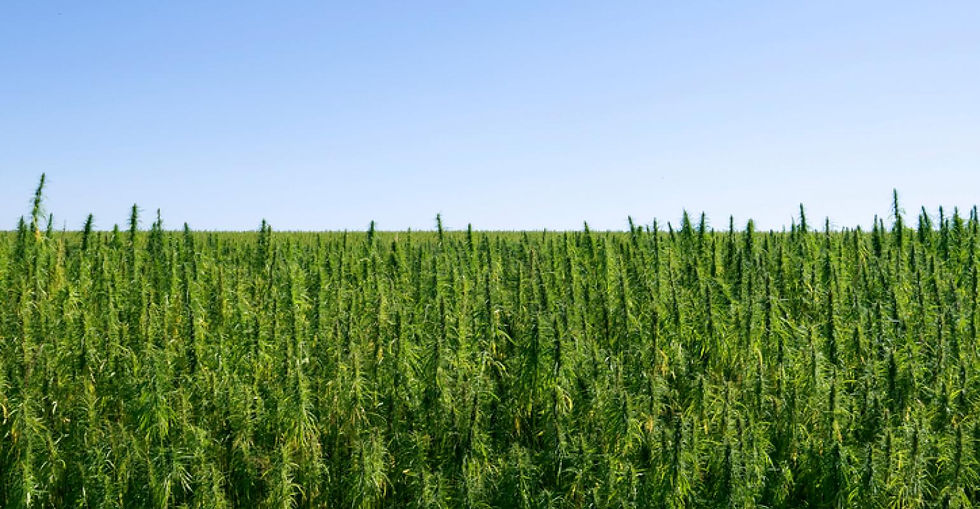
A hemp plantation, featuring the densely packed stems of Cannabis sativa.
Stinging nettle fibres are also extracted through the same process as flax, and are impacted by preconceived public notions like hemp, due to the skin irritation that the plant causes upon contact. Despite the discomfort caused by its stings, the nettle can be manufactured into luxurious fabrics similar to cotton, silk or linen.
Nettles require minimal water, and often zero pesticide usage
The plants thrive in poor soil and on steep cliffs, eliminating the need for fertilisers and herbicides, while also preventing soil erosion to maintain the natural ecosystems
The by-products of nettle fibre production can be utilised in other industries, including for cosmetic purposes, reducing waste
Left to right: Stinging nettle plants, processed nettle fibres, and nettle fabric of various colours.
Banana fibres are similarly obtained through a retting method, however generally employ the more time-intensive, chemical-free process. The fibres are sourced from the leaf sheaths of banana plants – both Abaca (non-edible) and Plantain varieties. Sheaths can be harvested gradually once the plant reaches maturity, and following fruiting, the entire plant can be harvested, as it will die at that stage regardless. The fibres can be manufactured into materials with similar characteristics to cotton, silk and linen.
Banana fibres utilise a by-product of the food industry, reusing a resource of which 1 billion tonnes are wasted annually
The plants have a fairly high fibre yield, with 37 kilograms of stems producing 1 kilogram of fibres
Banana plantations tend to require deforestation, and deplete the soil fertility, as well as causing erosion
Pesticides, herbicides and fertilisers are commonly required on banana crops, with agrochemical runoff polluting ecosystems
Depending on the geographical location of crops, banana plants can be grown without the need for irrigation, minimising water consumption
Left to right: A banana plantation, two men processing banana fibres after retting, and beige banana fabric.
Soysilk is manufactured from the by-products of soybean processing for the food industry. The soy protein fibres are extracted, chemically dissolved, and extruded from a spinneret into long filaments, before being woven or knitted into fabric. Soysilk bears similarities to silk, as the name suggests, as well as cashmere, producing soft, delicate fibres.
Soysilk utilises a waste product, maximising the output of soybean crops and the resources necessary to grow them
Deforestation is a prominent issue in the soybean industry, resulting in soil infertility, habitat loss, and the release of stored carbon
The process of manufacturing Soysilk requires chemicals – even occasionally involving formaldehyde, a possible carcinogen – however, the use of a closed-loop system to recycle chemicals limits harm and prevents their introduction into the environment
The ample use of pesticides and moderate need for fertilisers on soybean crops introduces harmful chemicals into the environment
Soybeans also have an extensive water consumption, resulting in a scarcity of the resource
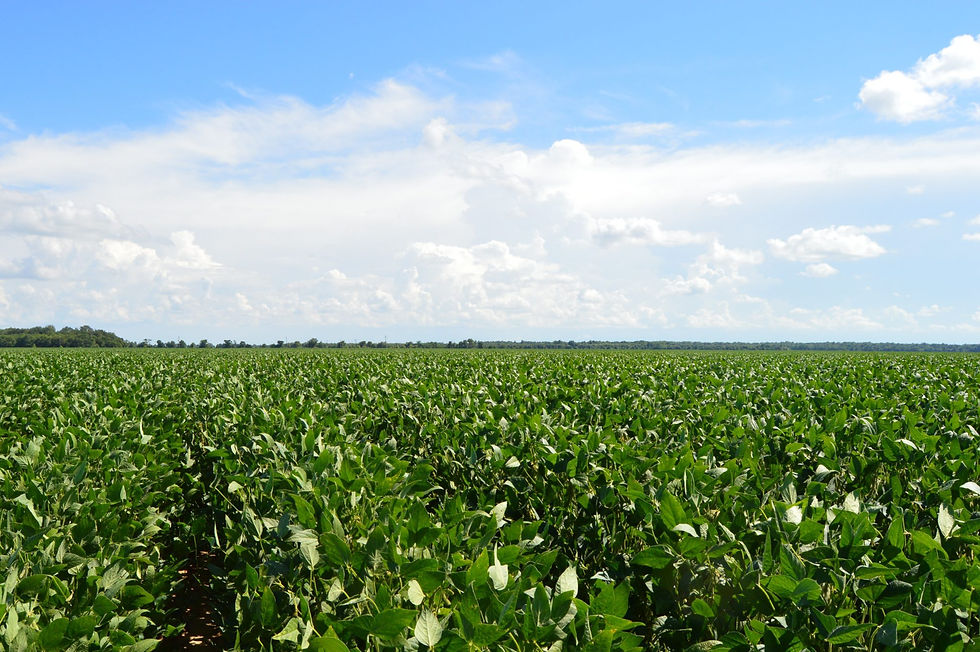
A field containing dense rows of soybean plants.
Orange fibre utilises the waste of citrus juice extraction – orange rinds – processing it in the same manner as other regenerated cellulose fibres. The resultant fibre is a silk alternative, with the addition of vitamin-enrichment from the natural oils in the citrus.
Orange fibre prevents the waste of over 1,000,000 tonnes food industry by-product from Italy alone
The orange trees rely on pesticides and fungicides, which contribute to environmental toxicity
Orange trees have a moderate water consumption, requiring irrigation
Oranges are perennial, commonly living for 30 years or more, and therefore land does not have to be continually cleared and the trees will retain carbon throughout their lifespan
There are chemicals present in the manufacturing process which can potentially damage the environment, with the employment of a closed-loop system not apparent
Left to right: Orange trees in a grove, orange peels discarded after juicing, and white fabric woven from orange fibres.
Fibres can also be manufactured from sour – or otherwise discarded – milk. This is achieved through the extraction of casein, a milk protein, which is then dehydrated and chemically dissolved, before being bonded into biopolymers which are extruded as filament fibres. The resultant material bears similarities to silk and wool.
The use of a waste product from an existing industry means that no additional resources are required to obtain the product for manufacturing
As the majority of milk is sourced from cows, there are deforestation, water consumption, and methane emission issues associated with milk fibre production
This process also requires chemicals, and it is unclear if a closed-loop system is utilised to prevent environmental contamination
Left to right: A dairy cow in a field, and QMilk Fabric, constructed from milk-derived fibres.
Pineapple fibres are unique in that they are used to produce woven, knitted, and non-woven fabrics. The fibres are derived from pineapple leaves, which are by-products of the food industry. The leaves are harvested and manually scraped to expose and extract the fibres (a process called ‘decortication’), before being washed, spun, and used to create fabric. Pineapple leather can be manufactured from the fibres through the method utilised for regenerated cellulose materials, however, the fabric is created as a non-woven film rather than individual filaments. Pineapple-derived materials are suitable alternatives to silk, cotton and leather.
The raw materials for pineapple fabrics are waste products, eliminating the need for excess environmental resources
Land consumption for pineapple crops has resulted in ample deforestation and habitat loss
The plants require heavy use of harmful pesticides, causing the contamination of water and soil
Decortication processes are performed by hand, without the use of chemicals or energy, therefore decreasing environmental impacts
Pineapple leather is manufactured in a closed-loop system, recycling resources which could potentially harm the planet
Pineapple plants have low water consumption, being drought tolerant
Waste biomass from pineapple textiles is transformed into biogas and fertiliser, establishing a zero-waste cycle
Left to right: Fruiting pineapple plants in a plantation, a man harvesting pineapple leaves, and white Piñatex pineapple leather.
Wine leather utilises the discarded skin and seeds of grapes used in winemaking to produce a substance very similar to leather with a natural deep red or burgundy colour. It is manufactured by drying the grape waste, which then undergoes chemical treatments to dissolve and polymerise the bio-oil and fibres, and is then formed as a sheet.
Wine leather is a high yield product, with 10 kilograms of grapes generating 2.5 kilograms of ‘grape marc’ (the by-product), which is capable of producing 1 square meter of leather
Utilising wine industry waste materials essentially increases the productivity of vineyards while maintaining the required resources
Wine leather be recycled at the end of the product’s lifespan, re-dissolving the material and creating new leather of the same quality
The colour of wine leather is limited to the natural hue of the grapes, minimising chemical usage
Wine grapes require significant quantities of pesticides, fungicides and fertilisers, which are damaging to ecosystems
Vineyards consume a significant amount of land and contribute to deforestation
The production of wine leather utilises chemicals, however, they are recovered and reused in a closed-loop system, preventing introduction and damage to the environment
Water is similarly recycled, conserving and limiting contamination of the precious resource
Left to right: Grapevines in a vineyard, grape marc, and Vegea wine leather.
Yeast leather it presents a far more sustainable option to animal-derived and synthetic leather, employing the fermentation of a specific strain of yeast to generate collagen protein – the primary component of leather – which is purified, before being compressed into a film, and tanned.
Yeast is sustained with glycerol from rapeseed, which is a beneficial crop, improving the drainage and structure of soil and restoring its nutrients
The tanning methods are still being developed; therefore, it is unclear as to whether chromium and other hazardous chemicals will be involved
Water consumption is not indicated for this fabric; however, it would likely be less than that of cow leather, with the possibility of water recycling due to the laboratory manufacturing facilities
Left to right: Petri dishes containing leather-growing yeast cultures, and Modern Meadow yeast leather.
Hopefully this introduction to fibre sustainability and innovations has enabled you to feel well-equipped with the knowledge to navigate fashion in a more eco-friendly way. As innovative fibres gain traction within the mainstream fashion industry and the importance of sustainability is further stressed, make sure you stay open, aware and curious for new developments. And get excited for next week’s post, which will be all about shopping – with a variety of price point and style options to suit your individual needs. As always, click over to @sustsained.style for some added bonuses and sneak peeks of upcoming posts.
For more insights into eco-friendly fibres, check out these sources:
Comentários